Transform Manufacturing KPIs into Real-World Wins
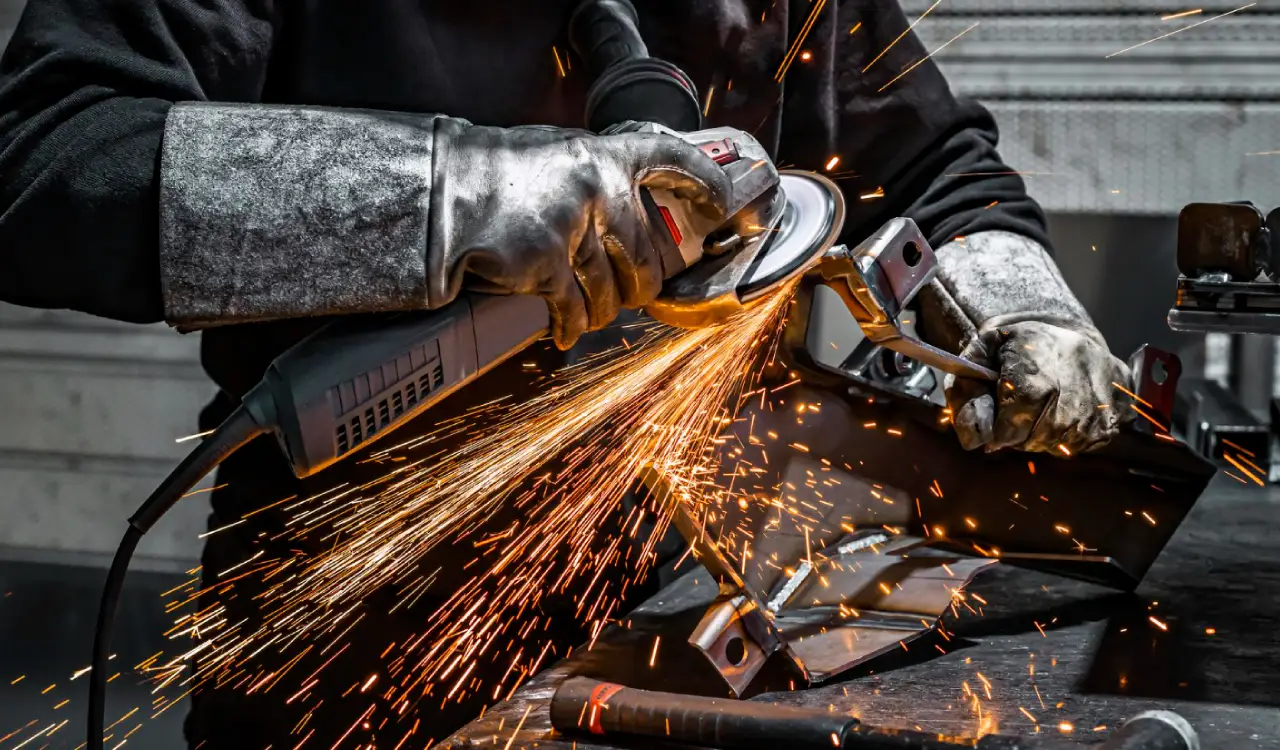
The global pandemic, increased reshoring, skilled labor crisis, geopolitical instability, changing laws, to name a few are some of the challenges currently facing supply chains across the world. As such, manufacturing KPIs (key performance indicators) have shifted from being mere benchmarks to keystones of supply chains that they are today; and agile, resilient supply chains have become the need of the hour.
With regard to the same, Deloitte’s 2024 Manufacturing Industry Outlook marks the need for manufacturers to embrace supply chain digitization, deeming it essential for enhancing supply chain performance, resilience, and tackling ongoing manufacturing challenges.
Supply chain digitization is the process of bringing together accurate data points and processes under one unified platform. Digitization provides end-to-end visibility and ensures that different supply chain tools integrate seamlessly.
Interested to know how you can digitize your supply chain? Connect with the experts at Syren Cloud here.
Understanding Manufacturing KPIs
Manufacturing KPIs are a reflection of company or supply chain performance goals. Monitoring them keeps companies informed about how well they are achieving their business outcomes and staying ahead of the competition. They play a key role in ensuring sustained success.
Read More: 70+ Manufacturing Metrics and KPIs Crucial for Optimizing Supply Chain Performance
The founders and supply chain experts at Syren, drawing from their decades of experience serving multiple Fortune 500 companies, have observed the make-or-break potential of manufacturing KPIs. They helped several clients achieve and surpass their KPI benchmarks that looked like:
- 1. Improving customer retention by 5%
- 2. Reducing expediting costs by 30%
- 3. Enhancing OTIF by 95%
- 4. Slashing cash-to-cash cycle time by 35%
- 5. Diminishing backorder rate to less than 1%
- 6. Cutting lost sales by 70%
- 7. Lowering transportation costs by 20%
- 8. Increasing overall ROI by 3x
Client Success Snapshot: OTIF
One of our clients is a multinational pharmaceutical conglomerate that faced complex challenges across multiple fronts: data integration, inventory management, and supplier alignment to name a few. Most importantly, they encountered obstacles in the timely and complete delivery of essential medical products, a cornerstone of their commitment to healthcare.
To strengthen their supply chain management, improve OTIF rates and address inventory challenges, the pharmaceutical giant collaborated with Syren. Syren empowered the pharmaceutical giant with the cutting edge capabilities of predictive analytics, optimized routing and real-time visibility into their supply chain.
By integrating Syren’s tailored OTIF solutions, the organization was able to significantly enhance delivery accuracy and efficiency by 95% and achieve operational success. In addition, they saw drastic improvements in:
- Operational and cost efficiency
- Demand planning precision
- Customer satisfaction and loyalty
At Syren, we are committed to supporting our clients to attain supply chain excellence. The following section is a brief outline of how we solve some of the most critical pain points of our clients in the manufacturing industry.
Syren Cloud’s Tailored Solutions for Achieving Manufacturing KPIs and Overcoming Pain Areas
The major challenges facing supply chain leaders in the manufacturing industry today include:
Pain Area 1: Spend Analysis
Spend analysis is the process of collecting, classifying, and analyzing expenditure data to decrease costs, improve operational efficiency, and enhance supplier relationships. It plays a vital role in the manufacturing supply chain by providing insights that can lead to better strategic sourcing and procurement decisions.
Challenges of Spend Analysis
- 1. Insufficient information on expenditure sources
- 2. Incorrect expense categorization
- 3. Data quality issues
- 4. Lack of standardization in categorizing expenses
- 5. Insufficient resources in collecting expense data
- 6. Poor analytics
- 7. Data inconsistencies due to silos in work cultures
Proposed Solution: Syren Cloud’s Control Tower
The Control Tower resolves the challenges stated above through:
Advanced ERP integration
Syren Cloud’s Control Tower seamlessly integrates with both internal and external ERPs. It onboards all the required data without your intervention. This way, the system creates comprehensive procurement analytics reports covering a wide range of data points and resolving data inconsistencies.
Powerful insights and recommendations
The system processes this data through advanced solutions like ATP, OTIF, CTD, etc., and gives out powerful insights and recommendations. Each procurement analytics report consists of information gathered from these integrations, offering insights into cost savings, supplier performance, compliance, and inventory information, which are crucial for precision decision making and proactively mitigating risks.
Centralized data hub and unified interface
Every report can be accessed with just a few clicks on the centralized hub, which contains all the data necessary for precision decision-making. Centralized access simplifies the data collection and analysis process.
Chat with the data in natural language
Syren Cloud’s Control Tower backed by LLM enables users (no previous experience required) to chat with the data, submit queries in natural language and instantly generate BI dashboards, plots and reports irrespective of how complex the data is. This allows companies to approach strategy meetings with a fresh perspective devoid of the time, data quality and complexity constraints.
End-to-end visibility
The Control Tower offers end-to-end visibility into the entire supply chain. 360-degree visibility into the supply chain resolves data quality and expense categorization challenges.
Pain Area 2: Supplier Management and Assessment
Supplier management and assessment involve the processes of selecting, evaluating, and monitoring suppliers to ensure they meet the company’s standards for quality, reliability, and cost-effectiveness. This practice is crucial in the manufacturing supply chain as it directly impacts product quality, compliance, production timelines, and overall operational efficiency.
Challenges of Supplier Management and Assessment
- 1. Evaluating supplier risk
- 2. Supplier capability assessment
- 3. Supplier performance analysis
- 4. Lack of timely business insights
- 5. High procurement costs
Proposed Solution: Syren Cloud’s Control Tower
Syren Cloud’s Control Tower is a comprehensive package of integrated solutions ranging from procurement to transportation. It leverages NLP and LLM technologies, and helps companies improve their analytics through advanced capabilities like ATP, CTD, OTIF, etc.
Control Tower resolves the challenges of supplier management and assessment stated above through:
Enhanced visibility
The Control Tower provides a complete overview of every element in your supply chain, from suppliers to logistics teams. You can choose to zoom into the procurement process and track orders, monitor supplier performance, and ensure timely raw material delivery.
Advanced analytical support
It is equipped with predictive analytics capabilities that sends alerts when delays or supplier shortages are to be expected. These technologies help proactively identify potential risks in the supply chain, from supplier disruptions to geopolitical issues, and develop mitigation strategies.
Cutting-edge marketplace solutions
The Control Tower features any array of high-end technologies like ATP, CTD, etc. In addition, you can also use it to evaluate suppliers’ performance based on various metrics like quality, delivery time, and cost, ensuring a reliable and cost-effective supply base.
Seamless ERP integration
By integrating with suppliers’ systems, it ensures data accuracy and provides insights into supplier reliability and cost-effectiveness, enabling better decision-making and risk management.
Pain Area 3: Supply Chain Visibility
Supply chain visibility allows companies to track and monitor all aspects of their supply chain in real time. This includes understanding the movement and status of goods from suppliers to production, through to delivery to the customer. Supply chain visibility helps enhance the operational efficiency, improves customer satisfaction through better delivery performance, and reduces the risk of delay and disruptions.
Challenges in Achieving End-to-End Supply Chain Visibility
- 1. Integrating diverse IT systems and technologies
- 2. Lack of data standardization across the supply chain
- 3. Data inconsistencies
- 4. High costs of implementing visibility solutions
- 5. Complex global supply chain networks
- 6. Rapid changes in market demands and supply chain disruptions
- 7. Limited expertise in analytics and data interpretation
- 8. Cybersecurity threats and data privacy concerns
Proposed Solution: Syren Cloud’s Control Tower
Syren Cloud’s Control Tower, short for Supply Chain Command Center, enables manufacturing companies to have a 360-degree view of the entire supply chain, from the starting point of the procurement process to the end point,i.e., until the products reach the customers. Every aspect of the supply chain can be closely monitored, and optimized for increased efficiency and effectiveness.
Control Tower resolves the challenges of supply chain visibility stated above through:
Effortless ERP integration
Syren Cloud’s Control Tower integrates with the ERP systems of your vendors and other middlemen seamlessly. No manual intervention is required to onboard the supply chain data from stakeholders. This streamlined data is used to provide detailed information and end-to-end visibility into all stages of the supply chain – procurement, inventory, manufacturing, sales & operations, and finally, transportation.
Agile and modular system
Dynamic global market scenario with ever-changing demands is one of the biggest challenges to implement supply chain visibility. With the Control Tower’s modular solutions built for agility, you can easily replace or add the desired modules (based on current requirement) without disrupting the entire architecture.
Ease of use
There is no formal training or prerequisite experience required to use the platform. Simply chat with the system in natural language and instantly access insights, generate BI dashboards, reports, plots and much more.
Rigid security and compliance
Robust protocols that comply with global standards (GDPR, HIPAA, SOC 2, ISO) ensure that there are no threats to data security.

Pain Area 4: Manufacturing Cost Management
Manufacturing cost management involves monitoring and analyzing the material, labor and other manufacturing overhead expenses to make informed business decisions.
Effective manufacturing cost management not only reduces these costs but also integrates closely with pricing management, supporting strategic discussions on product performance and viability. By improving visibility into manufacturing costs, businesses can better source materials, streamline processes, manage workforces, and reduce waste, leading to optimized margins and maximized profits.
Challenges of Manufacturing Cost Management
- 1. Fluctuating market dynamics
- 2. Supply chain disruptions
- 3. Changing raw material prices
- 4. Maintaining product quality while managing costs
Proposed Solution: Syren Cloud’s Control Tower
Syren Cloud’s Control Tower provides a complete package of integrated solutions for every stage of supply chain, from procurement to transportation. It employs NLP and LLM technologies, aiding companies in upgrading their analytics with advanced functionalities like ATP, CTD, OTIF, etc.
Syren Cloud’s Control Tower resolves the challenges of manufacturing cost management stated above through:
Superior analytics
Equipped with predictive analytical capabilities, the S3C proactively alerts stakeholders about potential delays or shortages from suppliers. These tools are crucial for identifying supply chain disruptions and mitigating risks early on and formulating effective countermeasures.
Powerhouse of insights and recommendations
The Control Tower processes data gathered from multiple points of the supply chain through advanced solutions like ATP, OTIF, CTD, etc., and generates high-quality reports, crucial for precision decision making and proactively protecting brand reputation. Each report consists of information gathered from these integrations, offering diverse strategic insights including those about cost savings while maintaining consistent product quality.
Flexible and adaptable architecture
Navigating the dynamic demands of the global market poses a significant challenge in achieving supply chain visibility. The Control Tower’s adaptable solutions are designed for flexibility, allowing for the easy addition or replacement of modules (as required by current needs) without affecting the overall system structure.
Pain Area 5: Demand Forecasting Accuracy
Demand forecasting involves predicting future customer demand for a product or service based on historical data, market trends, and other relevant factors. It enables businesses to make informed production and inventory management decisions, optimizing supply chain operations, reducing excess inventory and associated costs, and improving customer satisfaction by ensuring product availability.
Challenges in Achieving Higher Demand Forecasting Accuracy
- 1. Variability in customer demand
- 2. Limited historical data
- 3. Rapid changes in market trends
- 4. Complexity of product lines and SKUs
- 5. Difficulty in integrating data about external factors (e.g., economic indicators)
- 6. Reliance on manual forecasting processes
- 7. Lack of advanced analytical tools and expertise
- 8. Communication gaps within the supply chain
- 9. Forecasting for new products without historical data
Proposed Solution: Syren Cloud’s Demand Forecasting & Supply Planning
Syren Cloud’s Demand Forecasting & Supply Planning solution offers a full suite of integrated solutions relevant for every stage of the supply chain – procurement, inventory, manufacturing, sales and operations, and transportation. Utilizing NLP and LLM technologies, it assists organizations effortlessly respond to demand fluctuations through powerful analytical support.
The Demand Forecasting & Supply Planning solution resolves the challenges of achieving demand forecasting accuracy stated above through:
State-of-the-art analytical capabilities
1. State-of-the-art analytical capabilities: The solution notifies stakeholders of possible delays or supplier shortages through real-time alerts. AI-powered analytics provide insights and forecast recommendations that help reduce forecast biases. Companies can optimize forecasts to the highest degree possible with scenario planning, consider various potential scenarios and develop contingency plans for intelligent resource allocation. This enables them to align their resources with market demand, thereby enhancing demand forecasting accuracy, and profitability.
Seamless data collection
It integrates with your stakeholders’ ERPs, with no manual intervention required. It onboards volumes of historic data in no time and provides critical inputs for demand management. The system seamlessly collects, creates and manages sales opportunity information, promotional and marketing activities and merges them into the consensus plan. As such, the recommendations are based on real-time updates in market trends, changing demands and much more.
Centralized dashboard
Centralized dashboard: Post-collection, the system processes information on various product lines, SKUs, and inventory levels. It creates accurate short-, mid-, and long-term plans by analyzing statistical, causal, and econometric data. This knowledge model helps companies use both quantitative and qualitative data effectively. All this data is stored in a centralized hub, easily accessible through simple queries in natural language. This eliminates the data miscommunication, misinterpretation across the entire team.
Pain Area 6: Reducing Cost-to-Deliver (CTD)
Cost to Deliver (CTD) refers to the total expenses incurred by a company to deliver a product or service to the customer. This includes manufacturing, warehousing, transportation, and distribution costs. The advantages of understanding CTD include providing insights into the efficiency of the supply chain, identifying opportunities for cost reduction, enabling more accurate pricing strategies, and improving profit margins.
Challenges in Reducing CTD
- 1. Fluctuating fuel and transportation costs
- 2. Inefficiencies in logistics and distribution networks
- 3. Limited visibility into supply chain operations
- 4. Variability in demand impacting delivery schedules
- 5. Increasing customer expectations for fast and free delivery
Proposed Solution: Syren Cloud’s Cost-to-Deliver
Reducing CTD requires collaboration between all parties involved in all stages of the supply chain. This can be achieved through:
Internal and external data integration
The system onboards data from all sources such as supplier ERPs, warehouse management software, etc. This data is then processed along with your internal information through advanced algorithms to show a single, comprehensive, product-centric view of the total expenses incurred for making and moving goods.
Natural language queries
Be it the most efficient route of transportation, the amount of inventory you are holding at different warehouses or the carrying costs you are currently incurring, you can get all the answers, insights and recommendations to improve the situation through a simple chat with the system.
Advanced analytics
The solution drives consistency in information landscape through powerful analytics to analyze profitability, demand and trade-offs. Companies can gain data-backed insights into transportation, inventory, sustainability and customer service.
Ease of implementation
One of the most important benefits of Syren Cloud’s Cost-to-Deliver solution is that the system is completely cloud-based and gets ready to implement in a few weeks. Your teams require little to no time to get acquainted with its unified, user-friendly interface. Your teams enjoy the ease of multi-stakeholder, end-to-end collaboration effortlessly.
Pain Area 7: Inventory Management
Inventory management involves overseeing and controlling the ordering, storage, and use of components that a company uses in the production of the items it sells, as well as managing the quantities of finished products that are available for sale. It helps manufacturing companies reduce the cost of holding excess inventory, minimizing the risk of stockouts and production disruptions, optimizing the allocation of warehouse space, and improving cash flow by aligning inventory levels closely with demand.
Challenges of Inventory Management
- 1. Accurate demand forecasting
- 2. Overstocking or understocking
- 3. Managing inventory across multiple locations
- 4. Fluctuating supplier lead times
- 5. Obsolescence and spoilage of inventory
- 6. Integration of inventory management systems
- 7. Real-time inventory tracking and visibility
- 8. Adapting to market changes and consumer trends
Effective inventory management enables manufacturers to meet customer demand promptly and efficiently, enhancing customer satisfaction and operational efficiency.
Proposed Solution: Syren Cloud’s Control Tower
The inventory control tower resolves the challenges stated above through:
Advanced ERP integration
Syren Cloud’s Control Tower seamlessly integrates with both internal and external data sources like ERPs, WMS, etc. It onboards all the required data without any manual intervention. This way, the system creates comprehensive inventory management dashboards and reports encompassing a variety of data points like slow moving objects, potential demand fluctuations and much more.
Powerful insights and recommendations
The system processes this data through advanced solutions like ATP, OTIF, CTD, etc., and gives out powerful insights and recommendations. Reports consist of information gathered from these integrations, offering insights into details like inventory holding costs, savings, perishable products, etc. which are crucial for precision decision making and proactively mitigating risks.
Centralized data hub and unified interface
All the data is cleaned and stored in a centralized hub, thereby eliminating data inconsistencies across the supply chain. These reports can be accessed with just a few clicks on the centralized hub.
NLP-powered solutions
Syren Cloud’s LLM allows individuals (regardless of prior experience) to interact with data in a conversational manner and immediately produce BI dashboards, charts, and reports, irrespective of the complexity of data.
Note:
The challenges and proposed solutions mentioned below have been reported
based on
our experience of serving multiple F500 clients. If your current business goals do not
align with the ones mentioned here, please get in touch with
our support team to
customize a solution for your specific needs.
Elevating Your Manufacturing Success with Syren Cloud
Syren cloud’s comprehensive suite of supply chain analytics and visibility solutions can resolve a plethora of challenges faced by today’s manufacturing companies. They are aimed at increasing the overall efficiency, reducing costs and profitability of your business.
What’s more? Syren Cloud’s services are flexible and scalable. You can pick one centralized solution to take care of your every need or customize marketplace solutions based on your requirements. Our supply chain experts help you pick the right solutions as per your needs and business goals.