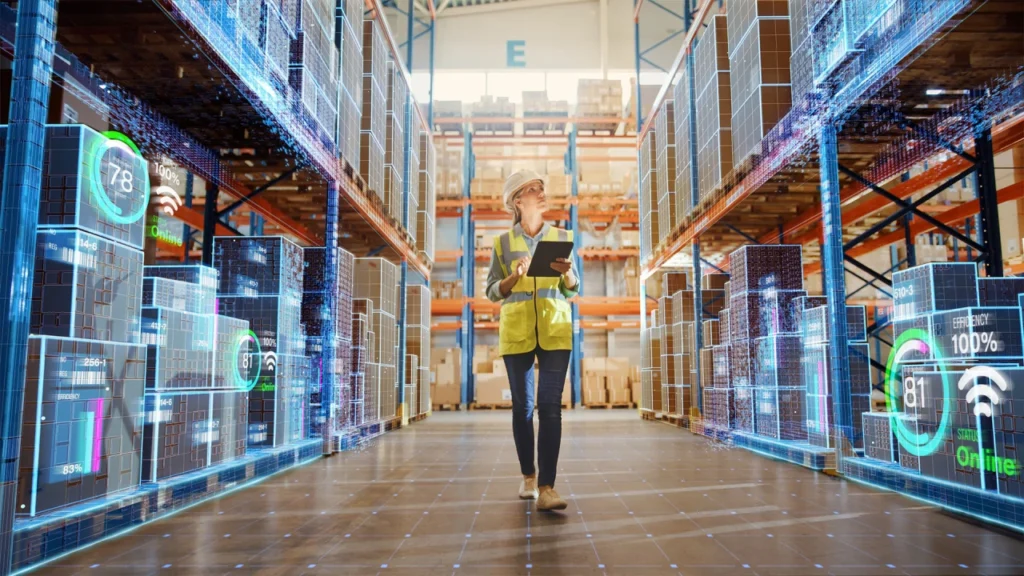
A resilient supply chain is more than just efficiently moving products from warehouse to customer. It’s about correctly planning and forecasting the resources, capacity, and supply strategically to meet fluctuating demand. When these elements fail to work in sync, companies experience stockouts, excess inventory, resource shortages, or production bottlenecks—all of which impact revenue and customer satisfaction.
Understanding Supply, Resource, and Capacity Planning
Though these three planning processes are deeply interrelated, they serve different purposes to build a resilient, disruption-free supply chain.
Supply Planning
Supply planning ensures that the right quantity of raw materials and finished goods are available to meet demand. It balances inventory levels, procurement schedules, and supplier reliability.
Resource Planning
Resource planning focuses on managing internal resources like workforce, materials, and equipment to maintain efficient operations. The right resource planning indicates that the production line is running smoothly, the warehouse workforce is adequate, and the machinery is maintained to prevent any unexpected maintenance failure.
Capacity Planning
Capacity planning is having the right number of resources at the right time. It determines whether a business has the necessary infrastructure, production capabilities, funds, and workforce to meet future demand.
Key Challenges in Planning: Why Many Businesses Struggle
Data Silos & Poor Visibility
Many companies still operate in silos, where supply, resource, and capacity decisions are made independently. This lack of cross-functional visibility results in poor warehouse management, inefficient workforce management, and inventory mismatches.
For example, a manufacturer may ramp up production based on outdated demand forecasts, only to find warehouses overflowing with unsold stock. Without real-time data integration, these mistakes can be costly.
On the other hand, companies that have started to leverage the capabilities of control towers have already seen a significant impact on their demand planning efficiency.
Complexities in Accurate Forecasting
Traditional forecasting methods often rely on historical data without accounting for real-time market trends. This can lead to inefficient supply management of raw materials or incorrect forecasts of seasonal demand spikes.
Take Black Friday sales, for instance. Retailers who miscalculate demand either run out of best-selling products (losing revenue) or end up with excessive post-holiday inventory (leading to markdown losses). Incorporating an AI-driven forecasting model that includes data visualization and reporting to generate actionable insights that drive smarter decisions.
Lack of Scalability
As business grows, planning processes that once worked may no longer scale. A common example is fast-growing e-commerce brands that scale too quickly without capacity planning. They end up with delayed deliveries, warehouse congestion, and fulfillment issues that damage customer trust.
Expanding enterprises need dynamic planning models that evolve with changing demand and operational complexity.
Supply Chain VolatilityÂ
Global supply chains are increasingly unpredictable owing to disruptions from geopolitical tensions, trade regulations, or supplier failures that derail even the most well-planned operations.
Businesses need agile planning systems that adjust dynamically in response to these disruptions.
Supply vs. Resource vs. Capacity Planning | Key Differences and When to Focus on What
When to Prioritize Supply Planning
If your company faces frequent stockouts or excess inventory, it’s a sign that supply planning needs improvement.
Optimizing procurement schedules and supplier collaboration can resolve these issues. For example, a company’s demand projects the need for a high product volume, its supply planning team must ensure the right balance between manufacturing and supplying the product to meet the demand.
Companies integrating AI and ML into their supply chains have been able to generate a data-driven demand plan that considers several factors like trends, events/holidays, locations, customer behavior, and more.
Businesses that have implemented AI-driven demand sensing and predictive analytics in supply chain planning have seen a 65% reduction in lost sales from stockouts and a 10-40% reduction in warehousing costs.
When to Prioritize Resource Planning
If labor shortages, material delays, or operational inefficiencies slow down production, resource planning should be optimized.
For a long time, ERP systems have been following the same strategy to manage and process the company data which involved manual input of data and put in a lot of expense in having a dedicated team or member for each task.
But the scenario has changed now! Companies have started to incorporate automated systems through control towers that leverage AI and ML models to do real-time demand sensing and forecasting. AI can even dynamically match workforce skills to operational needs, which reduces idle time significantly and improves resource allocation efficiency.
When to Prioritize Capacity Planning
If business growth is outpacing production capabilities or warehouse capacity, focusing on capacity planning helps avoid bottlenecks.
Supply chains have faced disruptions even when efficiently planning and managing capacity planning, because of varied data sources, changing customer behavior, cross-functional collaboration, etc. Meanwhile, thriving supply chains have started to implement demand planning software to perform demand sensing and predictive analysis for efficient capacity planning.
How AI, Automation, and Predictive Analytics have Advanced Supply Chain Management
Demand Sensing Using AI
Unlike traditional forecasting techniques, which rely on historical sales data, AI-powered demand sensing captures real-time signals from multiple sources—market trends, weather patterns, consumer behavior, and geopolitical events—to predict demand shifts with far greater accuracy.
For example, PepsiCo incorporates AI-driven demand sensing to adjust production schedules dynamically, ensuring that they produce the right quantities of beverages and snacks for each region, and reducing excess inventory and stockouts.
Optimizing Workforce and Inventory through Automated Resource Allocation
Resource planning has long been a complex challenge, requiring businesses to balance labor availability, raw material procurement, and operational costs. Automation streamlines this process by intelligently reallocating resources based on real-time needs.
For instance, Unilever uses automation to optimize raw material sourcing. If a specific ingredient faces supply constraints, the system automatically suggests alternative suppliers or adjusts production schedules to avoid disruptions. This level of adaptability reduces costs and ensures seamless operations.
Predictive Capacity Planning: Scaling for the Future
Capacity planning often struggles with overestimation (leading to wasted investment in facilities and equipment) or underestimation (causing production bottlenecks and lost sales). Predictive analytics helps companies model different scenarios, ensuring they scale operations in alignment with actual demand.
Look at Amazon’s fulfillment centers—the company uses predictive analytics to determine where to build new warehouses, how much storage capacity is needed, and where to position inventory to meet next-day and same-day delivery demands. This data-driven approach enables cost-effective expansion without overcommitting resources.
Breaking Down Silos for Real-Time Insights and End-To-End Visibility
AI and automation also help eliminate data silos, allowing for seamless integration across suppliers, manufacturers, distributors, and retailers. With real-time connectivity, businesses can proactively manage risks such as supplier delays or sudden demand surges.
For example, Tesla’s vertically integrated supply chain leverages AI-powered planning tools to monitor raw material availability, optimize production schedules, and adjust capacity dynamically. This integration helps the company navigate global chip shortages better than competitors, ensuring steady vehicle production.
Achieve Precision Planning with Syren Cloud
The best supply chains must move beyond reactivity and focus on being predictive. By integrating supply, resource, and capacity planning, businesses can minimize disruptions, optimize costs, and scale with intelligent, data-driven planning tools.
Connect with our experts today and take your supply chain planning to the next level with Syren Cloud!