70+ Manufacturing Metrics and KPIs for Optimizing Performance
- Introduction
- Manufacturing Metrics and KPIs: 101
- Examples of Manufacturing Metrics and KPIs
- 4 Things To Consider When Choosing the Right Manufacturing Metrics and KPIs for Your Business
- 18 Important Manufacturing KPIs to Track
- Production costs
- Production volume
- Production downtime
- Overall equipment effectiveness (OEE)
- Overall operations effectiveness (OOE)
- Total effective equipment performance (TEEP)
- Defect density
- Capacity utilization
- Rate of return (ROR)
- First time right (FTR)
- On-time delivery
- Asset turnover
- Unit costs
- Inventory turns
- Maintenance costs
- Return on assets
- Revenue per employee
- Profit per employee
- 5 Most Important KPIs That Ensure Manufacturing Success
- Types of Manufacturing Metrics
- 6 Manufacturing Metrics to Monitor Production Efficiency
- 11 Manufacturing Metrics to Monitor Cost
and Profitability
- Total manufacturing cost per unit excluding materials
- Manufacturing cost as a percentage of revenue
- Net operating profit
- Productivity in revenue per employee
- Average unit contribution margin
- Return on net assets (RONA)
- Energy cost per unit
- Cash-to-cash cycle time
- Earnings before interest, tax, depreciation and amortization (EBITDA)
- Projected customer demand
- Employee turnover
- 5 Manufacturing Metrics to Monitor Manufacturing Compliance
- 9 Manufacturing Metrics to Monitor Maintenance
- 5 Manufacturing Metrics to Monitor Customer Experience and Responsiveness
- 7 Manufacturing Metrics to Monitor the Quality of Production
- 7 Manufacturing Metrics to Monitor Lean Manufacturing
- 3 Manufacturing Metrics to Monitor Performance
- 2 Manufacturing Metrics to Monitor Innovation in Production
- Book a Demo!
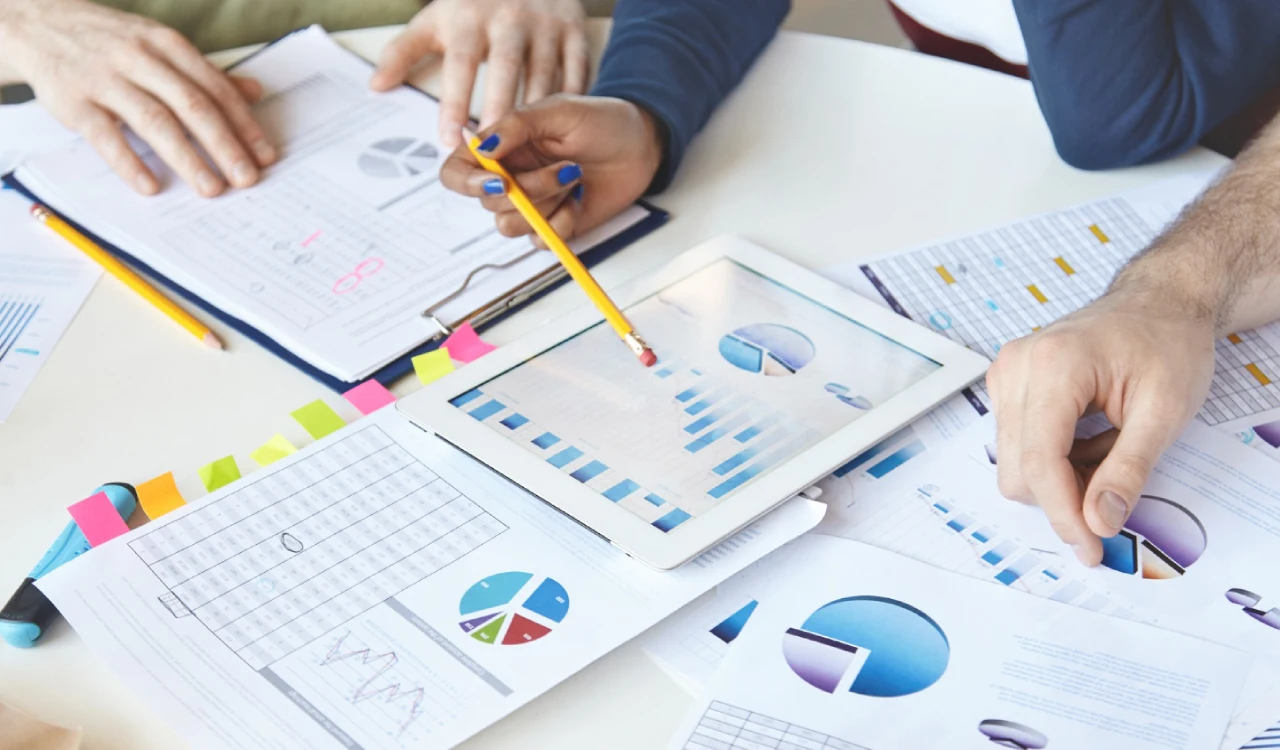
Manufacturing metrics and KPIs throw light on how well-oiled your manufacturing process is. They are crucial in assessing and enhancing the performance of your manufacturing supply chain.
Read More: Learn How To Transform Your Manufacturing KPIs Into Real-World Wins
This article is a comprehensive guide to manufacturing metrics and KPIs. We discuss the definitions of these metrics, guidelines on how to choose the right KPIs for your business and much more. We begin with the basics.
Manufacturing Metrics and KPIs: 101
What are manufacturing metrics?
Manufacturing metrics offer quantitative information about your production processes. This data can be used to evaluate and compare the efficiency of your manufacturing activities. These metrics support your manufacturing KPIs.
What are manufacturing metrics?
KPIs, short for Key Performance Indicators, are used to measure, analyze, compare and optimize the performance of your operations over a period of time. Manufacturing KPIs provide detailed insights into how your production processes align with the company’s goals.
What is the difference between manufacturing metrics and KPIs?
The difference between manufacturing metrics and KPIs is discussed as follows:
To illustrate how manufacturing metrics and KPIs are related, consider the example of OEE and Production Yield.
Production yield is a manufacturing metric that gives the number of acceptable goods produced in comparison to the total number of goods manufactured. It is expressed as a percentage and directly impacts the OEE (Overall Equipment Effectiveness) KPI.
OEE is a comprehensive KPI that represents the efficiency and effectiveness of a manufacturing process. A high yield indicates a high quality of production, suggesting fewer defects and wastage. However, OEE extends beyond just measuring output quality. It also includes how efficiently and effectively the manufacturing process operates as a whole and incorporates aspects of equipment uptime and performance speed.
While the production yield offers a focused view on one aspect of the manufacturing process, OEE uses this and other metrics to provide a comprehensive overview of production efficiency and effectiveness in relation to the company’s operational goals.
Examples of Manufacturing Metrics and KPIs
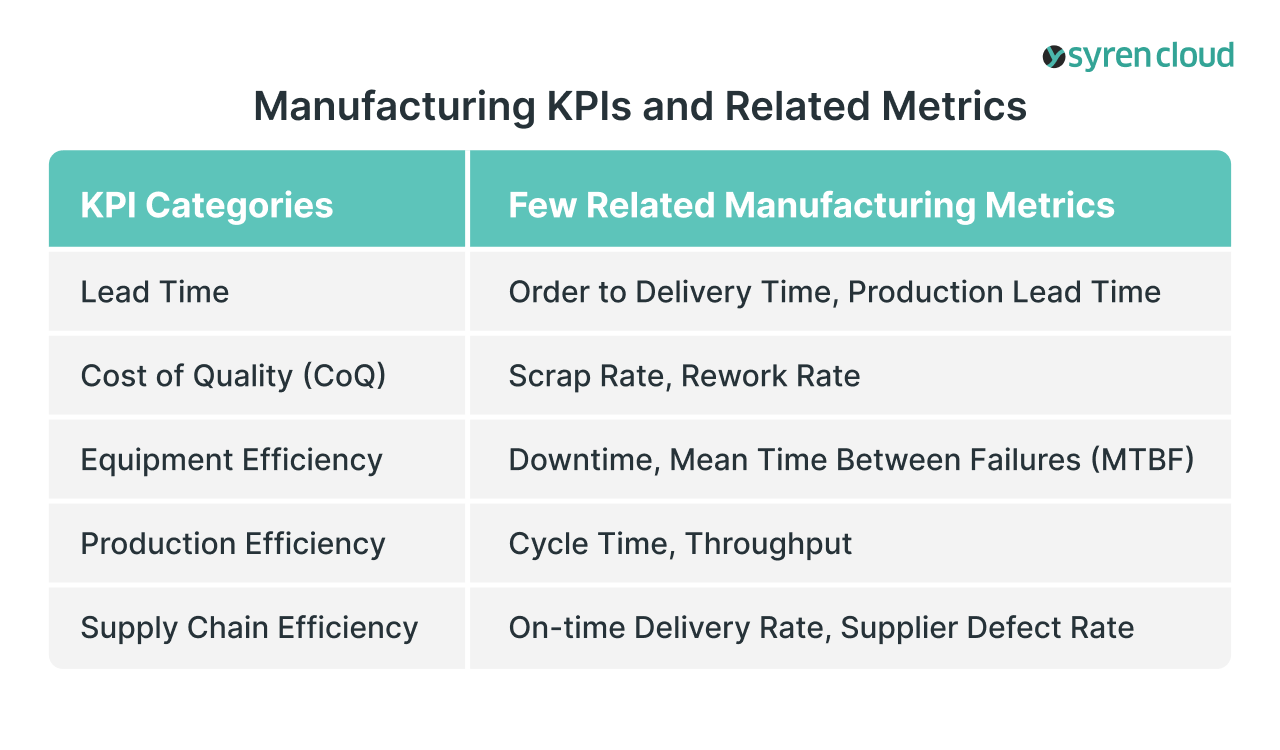
4 Things To Consider When Choosing the Right Manufacturing Metrics and KPIs for Your Business
1. They should demonstrate your business goals
The manufacturing metrics and KPIs you choose should ideally align with your overall business objectives. For instance, if your current business goal is to enhance the operational efficiency of your manufacturing supply chain:
Goal: Increased Operational Efficiency
Relevant KPI: Customer Satisfaction Score (CSS)
Meaning
CSS measures the level of satisfaction customers have with the company’s products, often obtained through surveys and feedback mechanisms.
Strategic Importance
Monitoring CSS helps you identify the areas for improvement in product quality and service, which are crucial to customer retention and loyalty.
Relevant Metric: Defect Rate
Meaning
The percentage of products that fail to meet quality standards out of the total products manufactured.
Strategic Importance
Defect rate is a reflection of production quality. By measuring defect rate, companies can improve the product quality and thus positively impact the CSS.
2. They should be actionable
The metrics and KPIs chosen should be able to provide you with an accurate way to measure the progress. Actionable metrics and KPIs not only measure progress but also guide decision-making and operational improvements. For instance, if your current business goal is to reduce production costs:
Goal: Reduced Production Costs
Relevant KPI: Cost Per Unit (CPU)
Meaning
CPU encompasses all costs involved in the production process, including materials, labor, and overhead.
Actionability
Tracking CPU can help you detect trends in production costs and pinpoint areas where manufacturing efficiency can be improved. A rising CPU cost may indicate the need to review supplier contracts, reassess production schedules, and invest in more efficient technology.
Relevant Metric: Scrap Rate
Meaning
Scrap rate is expressed as the percentage of materials used in production that do not result in a sellable product. It directly impacts material costs and, consequently, the Cost per unit.
Actionability
Analyzing scrap rate can help companies identify inefficient production processes. This information can then be used to adopt techniques to reduce waste such as improving material handling, employee training or upgrading equipment. A reduction in scrap rate leads to lower CPU.
3. The necessary data collection should be feasible
The manufacturing metrics or KPIs you choose should have clearly defined data sources that are capturable by ERPs. For instance, if your current business goal is to manage your inventory well:
Goal: Improved Inventory Management
Relevant KPI: Inventory Turnover Ratio
Meaning
The inventory turnover ratio measures how many times a company’s inventory is sold and replaced over a given period of time. A lower ratio suggests overstocking or insufficient sales.
Data Collection Feasibility
This KPI relies on data that is readily available to capture. The ERP system tracks the cost of goods sold (COGS) and the average inventory during the period necessary to calculate the inventory turnover ratio.
Relevant Metric: Days On Inventory On Hand (DOI)
Meaning
DOI indicates the average number of days that inventory remains in stock before being sold.
Data Collection Feasibility
DOI can be easily calculated by using the data on inventory levels and sales typically maintained in an ERP system.
4. They should have an efficient reporting system
The right manufacturing metrics and KPIs are easy to report through consolidated and configurable dashboards. For instance, if your current business goal is to enhance production efficiency:
Goal: Enhanced Production Efficiency
Relevant KPI: Overall Equipment Effectiveness (OEE)
Meaning
OEE is a comprehensive measure of manufacturing productivity that combines availability, performance, and quality to provide a single performance indicator for how effectively equipment is being used.
Reporting Feasibility
The visual representation of OEE enables quick identification of underperforming areas and facilitates prompt intervention. ERP systems can pull up OEE scores for each manufacturing line through dashboards. However, this is often time-taking.
Advanced supply chain analytics solutions like Syren Cloud’s Control Tower can accomplish the same in a matter of seconds. You can also promptly configure the dashboards to show historical trends, breakdowns of the three components (availability, performance, quality), and comparisons against benchmarks or targets.
Relevant Metric: Downtime Analysis
Meaning
This metric tracks the amount and reasons for equipment downtime, categorizing it into scheduled maintenance, unscheduled breakdowns, changeovers, etc.
Reporting Feasibility
With configurable dashboards, downtime analysis can be reported in real-time, highlighting the most common causes of stoppages and their impact on production. By integrating this data into the OEE dashboard, stakeholders can drill down into specific issues affecting equipment effectiveness, prioritize maintenance activities, and implement preventive measures.
Note:
The manufacturing metrics and KPIs discussed above are only for
illustrative
purposes. Each business goal can have more than one relevant KPI and metric.
18 Important Manufacturing KPIs to Track
To recall what are KPIs in manufacturing: They help you evaluate productivity, quality, profitability and customer satisfaction. Various KPIs can be used to improve the operational efficiency across your manufacturing supply chain.
The KPIs discussed in the section are listed as follows:
- Production Costs
- Production Volume
- Production Downtime
- Overall Equipment Effectiveness (OEE)
- Overall Operations Effectiveness (OOE)
- Total Effective Equipment Performance (TEEP)
- Defect Density
- Capacity Utilization
- Rate Of Return (ROR)
- First Time Right (FTR)
- On-time Delivery
- Asset Turnover
- Unit Costs
- Inventory Turns
- Maintenance Costs
- Return On Assets
- Revenue Per Employee
- Profit Per Employee
Production Costs
Manufacturing a product incurs various expenses, known as production costs. These encompass direct costs like labor and raw materials, as well as indirect costs, including overhead and rent.
Production Volume
Production volume quantifies the number of units produced within a given period. It is essential for evaluating manufacturing efficiency benchmarks. This KPI helps gauge the overall production capacity of your factory.
Production Downtime
Production downtime tracks the duration when a factory’s production lines are inactive. It includes both scheduled and unexpected stoppages. To enhance productivity, it’s crucial to reduce and manage the periods when production lines are halted.
Overall Equipment Effectiveness (OEE)
OEE represents the proportion of time your facility is effectively producing high-quality products efficiently and without interruptions. OEE is determined by the following factors:
- Availability
The actual production time represented as a percentage of the scheduled operating time. - Performance
The rate at which your equipment or facility operates at its maximum capacity, expressed as a percentage. - Quality
The percentage of units produced that meet quality standards out of the total units initiated.
OEE primarily assesses the duration a production line is in operation relative to its optimal potential capacity. Plant managers frequently utilize this KPI to benchmark the overall performance of similar production resources and determine the effectiveness of plant operations. Additionally, OEE serves as a fundamental metric for monitoring improvements in eliminating inefficiencies as part of ongoing process enhancement efforts.
Overall Operations Effectiveness (OOE)
OOE comprises three components:
- Availability
The actual production time represented as a percentage of the total available operation time, maintenance included. - Performance
The proportion of time your equipment or facility operates at maximum capacity. - Quality
The percentage of quality products made out of the total units initiated.
OOE is similar to OEE. However, it differs in how availability is calculated. OEE does not include time for machine maintenance. On the other hand, OOE includes availability calculation.
Total Effective Equipment Performance (TEEP)
TEEP is expressed as a percentage and is used to measure utilization. It shows what your facility could potentially achieve when it operates non-stop for 24 hours a day, every day of the year, while consistently manufacturing high quality products.
TEEP comprises three components:
- Availability
The actual production time as a percentage of the total time, assuming the plant operated continuously 24/7 throughout the year. - Performance
The proportion of time your equipment or facility operates at its highest capacity. - Quality
The percentage of started units that are produced to quality standards out of the total units initiated.
Defect Density
Defect density is a quality metric that monitors the quantity of defective products relative to the total amount of products produced. Defects can adversely affect profit margins and lead to issues with customer satisfaction.
Capacity Utilization
Capacity utilization evaluates the extent to which a plant’s total potential capacity is being utilized. This KPI is useful for gauging efficiency and serves as a sign of potential opportunities for expansion.
Rate Of Return (ROR)
Rate of return is a financial metric that assesses the performance of a capital expenditure or investment over a duration. It is represented as a percentage and considers the gains or losses generated by an investment throughout a specified period.
First Time Right (FTR)
First time right is a metric aligned with the Six Sigma objective of executing processes correctly from the outset, consistently. It aids plant managers in striving for streamlined and lean production activities.
On Time Delivery
On-time delivery measures the proportion of products that reach customers by the agreed deadline relative to the overall quantity of products shipped.
Asset Turnover
Asset turnover tracks how effectively equipment and assets are utilized to generate income. A higher ratio of asset turnover signifies operational efficiency. Optimal turnover ratios differ across sectors.
Unit Costs
Unit costs, also referred to as cost of goods sold (COGS), represent the average expense incurred in producing a single product unit.
Inventory Turns
This critical inventory management metric assesses the consumption and replenishment rate of inventory over a specified timeframe. Plant managers focused on lean manufacturing initiatives aim to keep inventory levels as low as possible.
Maintenance Costs
Maintenance expenses encompass all costs associated with both preventive and corrective actions to upkeep and fix production machinery. This KPI tracks a machine’s performance longitudinally, aiming to maximize equipment uptime while minimizing expenses.
Maintenance unit cost represents the overall maintenance costs needed to manufacture a single product unit within a designated period.
Return On Assets
Return on assets evaluates the profitability of your company based on its assets. This KPI reflects how effectively assets are utilized to generate revenue.
Revenue Per Employee
Revenue per employee calculates the average amount of income produced by each employee. This KPI is useful for tracking performance over time and comparing it with peer companies.
Profit Per Employee
Similar to revenue per employee, this KPI examines the average profit made per employee. It serves as an effective indicator of your organization’s overall profitability.
5 Most Important KPIs That Ensure Manufacturing Success
As discussed above, there are multiple manufacturing metrics and KPIs that companies can monitor to optimize their supply chains. The top 5 KPIs include:
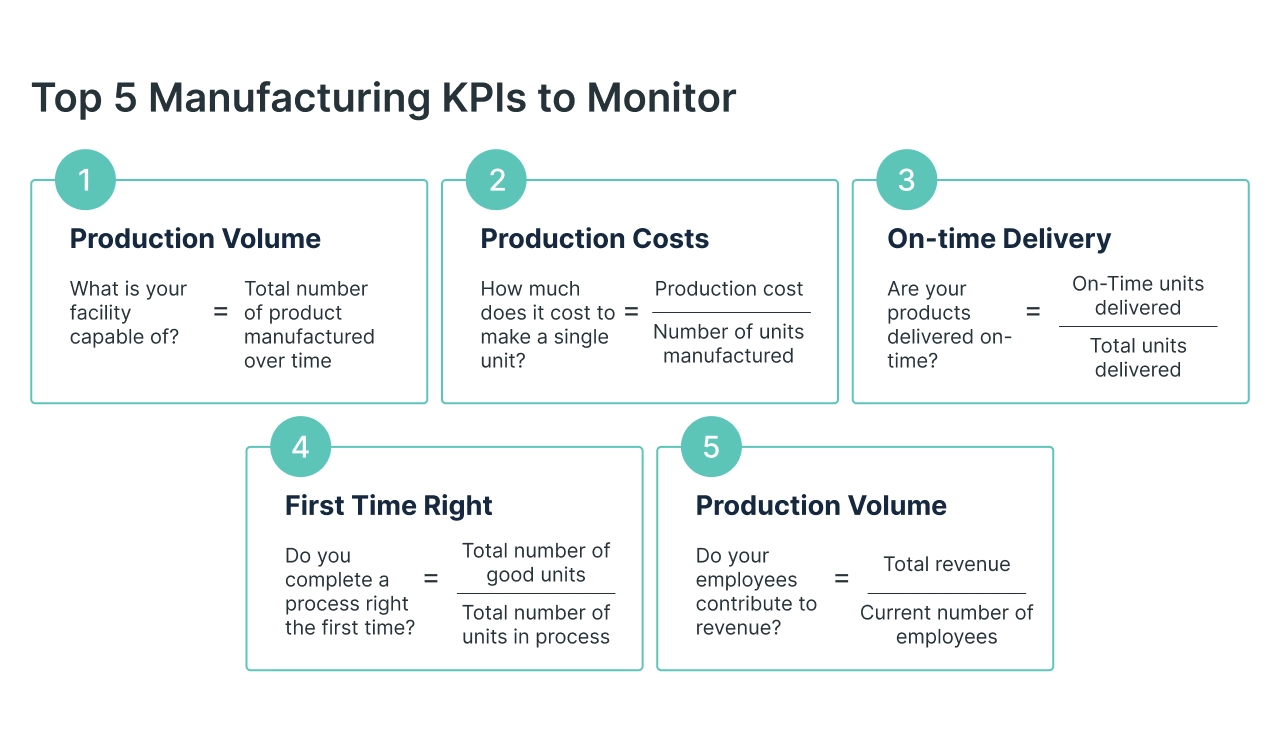
Types of Manufacturing Metrics
There are different types of manufacturing metrics. They include:
- 1. Metrics that monitor efficiency
- 2. Metrics that monitor cost and profitability
- 3. Metrics that monitor manufacturing compliance
- 4. Metrics that monitor maintenance
- 5. Metrics that monitor customer experience and responsiveness
- 6. Metrics that monitor quality of production
- 7. Metrics that monitor lean manufacturing
- 8. Metrics that monitor performance
- 9. Metrics that monitor innovation in production
6 Manufacturing Metrics to Monitor Production Efficiency
Manufacturing efficiency emphasizes maximizing resources and minimizing costs. High efficiency translates to generating the highest quality product for the least expense. The KPIs for efficiency in manufacturing concentrate on optimal processes, eliminating waste.
There are six metrics that are used to keep track of production efficiency:
- Throughput
- Work in process (WIP)
- Schedule or production attainment
- Scrap material value
- On standard operating efficiency
- Asset utilization
Throughput
Throughput quantifies the amount of product produced during a given period. It is used for analysis and comparison of similar machinery, production lines, or manufacturing facilities.
Work in process (WIP)
Work in process encompasses items that are partially produced or awaiting completion and sale. It covers the costs of raw materials, labor, and overhead for goods that are not yet finished. It offers insights into the efficiency of material use and the worth of goods in progress.
Schedule or production attainment
Schedule attainment evaluates the actual production volume against the projected output.
Scrap material value
Scrap material is the surplus material remaining once a product has been finished.
On standard operating efficiency
When employing a piece rate or incentive system, comparing real performance to the anticipated labor expenses factored into your product pricing is known as on standard operating efficiency. This approach aids in monitoring labor expenses, enabling adjustments to product pricing or the identification of more efficient methods to reduce production costs.
Asset utilization
Also referred to as the average return on assets, asset utilization examines the efficiency with which your assets are employed in production.
11 Manufacturing Metrics to Monitor Cost and Profitability
Financial and profitability KPIs assist in gaining a deeper insight into product costs. There are 11 metrics that are used to keep track of costs and profits:
- Total manufacturing cost per unit excluding materials
- Manufacturing cost as a percentage of revenue
- Net operating profit
- Productivity in revenue per employee
- Average unit contribution margin
- Return on net assets (RONA)
- Energy cost per unit
- Cash-to-cash cycle time
- Earnings before interest, tax, depreciation and amortization (EBITDA)
- Projected customer demand
- Employee turnover
Total manufacturing cost per unit excluding materials
Enhancing efficiency isn’t limited to just purchasing materials at a reduced cost but also involves closely examining and monitoring labor and overhead expenses.
Manufacturing cost as a percentage of revenue
The ratio of manufacturing cost to revenue evaluates the total production expenses against the income generated. This KPI is useful for assessing similar production facilities and pinpointing potential areas for cost reduction.
Net operating profit
Net operating profit, a key profitability indicator, can be applied to a specific facility, business division, or the entire company. It’s calculated by deducting the cost of goods sold, operating expenses, interest, and taxes from total revenue.
Productivity in revenue per employee
Revenue serves as a significant indicator of productivity and can be applied to a particular plant, business unit, or used as a metric across the entire company.
Average unit contribution margin
The contribution of a product refers to the amount of profit left to cover fixed expenses after all the variable costs per unit are accounted for. This metric is essential for identifying production lines that are underperforming.
Return on net assets (RONA)
Return on net assets (RONA) measures the net income produced as a percentage of the company’s assets, offering insights into how effectively the organization uses its assets to generate profit. It emphasizes the use of fixed assets, such as equipment and materials, in revenue generation.
Energy cost per unit
The energy cost per unit tracks the amount of energy required to produce each unit, with the energy expense influencing the profitability of various product lines.
Cash-to-cash cycle time
The duration required to transform investments in inventory into cash flow from sales is a crucial measure of financial efficiency.
Earnings Before Interest, Taxes, Depreciation, and Amortization (EBITDA)
EBITDA stands as a critical metric used by investors to compare companies, offering an alternative view of operational profitability distinct from net earnings.
Projected customer demand
Forecasting customer demand utilizes past data and current market trends to predict future needs, aiding in supply chain optimization. Strategic use of ERP tools facilitates precise inventory forecasting, balancing stock levels with customer demand while minimizing storage costs.
Employer turnover rate
A high employee turnover rate can adversely affect the bottom line due to the costs associated with recruiting, training, and integrating new staff. Monitoring attrition rates is vital for identifying the need for improvements in company culture, training, and career development opportunities to enhance employee retention.
5 Manufacturing Metrics to Monitor Manufacturing Compliance
These KPIs oversee risks related to business, finance, legality, and reputation. They also encompass compliance with employment law through metrics for health, safety, and environmental standards, in addition to ensuring product safety and the privacy of consumer data.
There are five metrics that are used to keep track of costs and profits:
- Reported Health and Safety Incidents
- Health and Safety Incidence Rate
- Reportable Environmental Incidents
- Number of Non-Compliance Events per Year
- Failed Audits
Reported Health and Safety Incidents
The metric for reported health and safety incidents logs the total count of safety and hazard events that must be reported to the Occupational Safety and Health Administration (OSHA) over a certain period.
Health and Safety Incidence Rate
The health and safety incident rate calculates the incidents of work-related injuries for every 100 full-time employees within a year-long period, known as the total case incident rate (TCIR).
Note: 200,000 = 100 employees working 40 hours per week, 50 weeks per year
Reportable Environmental Incidents
Reportable environmental incidents track the quantity of environmental issues that a company is obligated to report to the Environmental Protection Agency (EPA), including concerns related to air and water quality, recycling, and more.
Number of Non-Compliance Events per Year
The metric for the number of non-compliance events annually documents instances where a manufacturing facility fails to meet established guidelines, recording the occurrence, cause, and solution for each event within a 12-month cycle.
Failed Audits
Regular safety audits in all manufacturing areas and equipment are essential, and tracking failed audits measures the frequency at which operations do not meet compliance standards.
9 Manufacturing Metrics to Monitor Maintenance
These metrics evaluate the effectiveness of maintenance initiatives in enhancing the performance of equipment, boosting uptime, and lowering expenses. They also consider the accessibility of equipment on the production line.
There are nine metrics that are used to keep track of maintenance:
- Maintenance unit cost
- Mean time between failure (MTBF)
- Mean time to failure (MTTF)
- Percentage maintenance planned (PMP)
- Percentage Planned vs. Emergency Maintenance Work Orders
- Unscheduled downtime
- Downtime in Proportion to Operating Time
- Avoided Costs
- Machine Set-Up Time
Maintenance unit cost
Track the expense of maintaining equipment against the quantity of units produced. This metric encompasses all expenses involved in keeping and fixing equipment to guarantee its dependable functioning. Utilize this KPI to assess the effectiveness of a machine over time.
Mean time between failure (MTBF)
MTBF assesses the average duration between failures of equipment, for instance, problems with a conveyor belt or an industrial valve. This metric offers insights into the dependability of your manufacturing assets.
Mean time to failure (MTTF)
MTTF, closely related to MTBF, focuses on components that cannot be repaired, like electronic parts or circuit breakers that need to be replaced upon failure.
Percentage maintenance planned (PMP)
Evaluate the overall hours spent on repairing and maintaining production equipment against the anticipated time required.
Percentage Planned vs. Emergency Maintenance Work Orders
Assess the proportion of maintenance that is scheduled versus that which arises due to emergencies. Emergency maintenance disrupts both workers and production. Plant managers might opt for a corrective maintenance approach for non-essential machinery or parts to address issues after unexpected downtime incidents.
Unscheduled downtime
This measures the duration for which equipment was intended to operate but was unable due to reliability or mechanical problems. Unscheduled downtime can lead to lost clients and income. It serves as an effective measure to evaluate the efficacy of maintenance strategies.
Downtime in Proportion to Operating Time
This ratio measures the amount of time equipment is idle compared to its operating time, for any reason.
Avoided Costs
These are the savings achieved through preventive maintenance efforts. Investing in regular maintenance prevents expensive fixes and extensive unplanned downtime.
Machine Set-Up Time
This refers to the duration required to prepare equipment for the next production cycle after finishing a batch.
5 Manufacturing Metrics to Monitor Customer Experience and Responsiveness
Manufacturing is crucial in ensuring the timely delivery of superior quality products, one of the essential elements for a remarkable customer experience.
There are five metrics that are used to keep track of maintenance:
On-time delivery to commit
This KPI evaluates the frequency with which manufacturing fulfills its delivery promises. It monitors the productivity of production lines and the rate at which product delivery timelines are met.
Lead time
Lead time assesses the duration from when orders are placed to when customers receive them.
Customer fill rate
Monitor how effectively customer demands are met using the available inventory of products. This KPI reflects the organization’s ability to satisfy customer needs promptly.
Customer return rate
Consider the proportion of business derived from returning customers. This serves as an effective measure for tracking customer retention and loyalty.
Customer satisfaction
Determining customer satisfaction begins with direct inquiry. Conduct customer satisfaction surveys to learn if customers are happy with your products and services, and if they would recommend your business to others.
7 Manufacturing Metrics to Monitor the Quality of Production
These KPIs serve as leading indicators for production performance, tracking defects at every stage of the production cycle.
Measuring manufacturing quality involves Quality KPIs like yield, perfect order percentage, and customer reject rate, which evaluate the degree to which products conform to their intended specifications.
There are seven metrics that are used to keep track of production quality:
- Yield
- First time yield
- Perfect order percentage
- Return merchandise authorizations (RMA)
- Customer reject rate
- Supplier’s quality incoming
- Scrap rate
Yield
Yield quantifies the total amount of finished products produced relative to the amount of raw materials used. It overlooks inefficiencies like rework or scrap.
First time yield
First time yield evaluates product quality by quantifying the units produced without defects and without the need for additional rework. It’s a predictive measure of issues in manufacturing processes, such as the quality of materials or equipment functionality.
Perfect order percentage
This KPI measures the proportion of total orders that are fulfilled on time without any problems, including late shipments, damaged goods, or incomplete orders. It helps assess the effectiveness of order processing, manufacturing, and delivery systems.
Return merchandise authorizations (RMA)
This tracks the frequency with which customers express dissatisfaction and are granted a refund for returned merchandise.
Customer reject rate
This rate identifies the number of components found defective by customers out of the total delivered. It further breaks down the analysis to individual parts, highlighting the parts rejected by customers.
Supplier’s quality incoming
A crucial supply chain KPI, this metric scrutinizes the quality of raw materials received from suppliers.
Scrap rate
This rate calculates the quantity of materials discarded during the production process. Reducing scrap not only saves costs by optimizing the use of raw materials but also reduces labor and time spent in selling, recycling, or disposing of scrap material.
7 Manufacturing Metrics to Monitor Lean Manufacturing
Measuring manufacturing efficiency involves the use of lean manufacturing KPIs, which are metrics designed to analyze and enhance process efficiency. Lean KPIs enable the identification of areas for waste reduction and speed enhancement.
There are seven metrics that are used to keep track of maintenance:
- Cycle time
- First pass yield
- Capacity utilization
- Machine downtime rate
- Downtime in proportion to operating time
- Material yield variance
- Overtime rate
Cycle time
Cycle time assesses the average duration needed to fulfill a customer order, offering insights into your business’s capability to satisfy customer demands.
First pass yield
First pass yield is a crucial indicator of product quality, highlighting the quantity of products made correctly on the initial attempt without the need for additional fixes. It serves as an early warning of potential manufacturing process issues.
Capacity utilization
Capacity utilization quantifies the extent to which a facility’s production capabilities are being employed, providing a measure for evaluating operational efficiency and potential for expansion.
Machine downtime rate
Machine downtime tracks the duration equipment remains idle and unable to produce, encompassing both scheduled and unscheduled maintenance or equipment breakdowns.
Downtime in proportion to operating time
This metric tracks how often production assets are operational versus idle due to maintenance, offering a metric for assessing the efficiency of manufacturing equipment.
Material yield variance
Material yield variance calculates the difference between the actual material consumed and the standard expected usage.
Overtime rate
The overtime rate quantifies the additional hours worked by employees beyond their regular schedule, indicating the extent of extra labor required.
3 Manufacturing Metrics to Monitor Performance
Calculating production KPIs involves tracking the effectiveness of each production stage. Manufacturing performance or production metrics gauge the success of various production phases, encompassing production attainment, changeover time, and takt time.
There are seven metrics that are used to keep track of maintenance:
Production attainment
This metric evaluates the capability of manufacturing to achieve its planned production goals. A higher attainment score indicates superior performance.
Changeover time
This indicates the duration required to switch a production line from producing one item to another.
Takt time
Takt time represents the necessary pace of production to satisfy customer demand, determined by dividing the customer demand by the time available for production.
2 Manufacturing Metrics to Monitor Innovation in Production
Keep track of and disseminate these metrics to foster innovation. Innovations might involve fresh or enhanced products, and could capitalize on process advancements or novel technologies, like artificial intelligence for manufacturing.
There are two metrics that are used to keep track of maintenance:
Rate of new product introduction (NPI)
This metric gauges the frequency at which your company launches new products into the market, focusing on the NPI rate for newly marketed products.
Engineering Change Order Cycle Time
This metric tracks the duration required to complete a product modification from the receipt of the change order to its execution, typically calculated as the average number of days needed to effectuate the change.