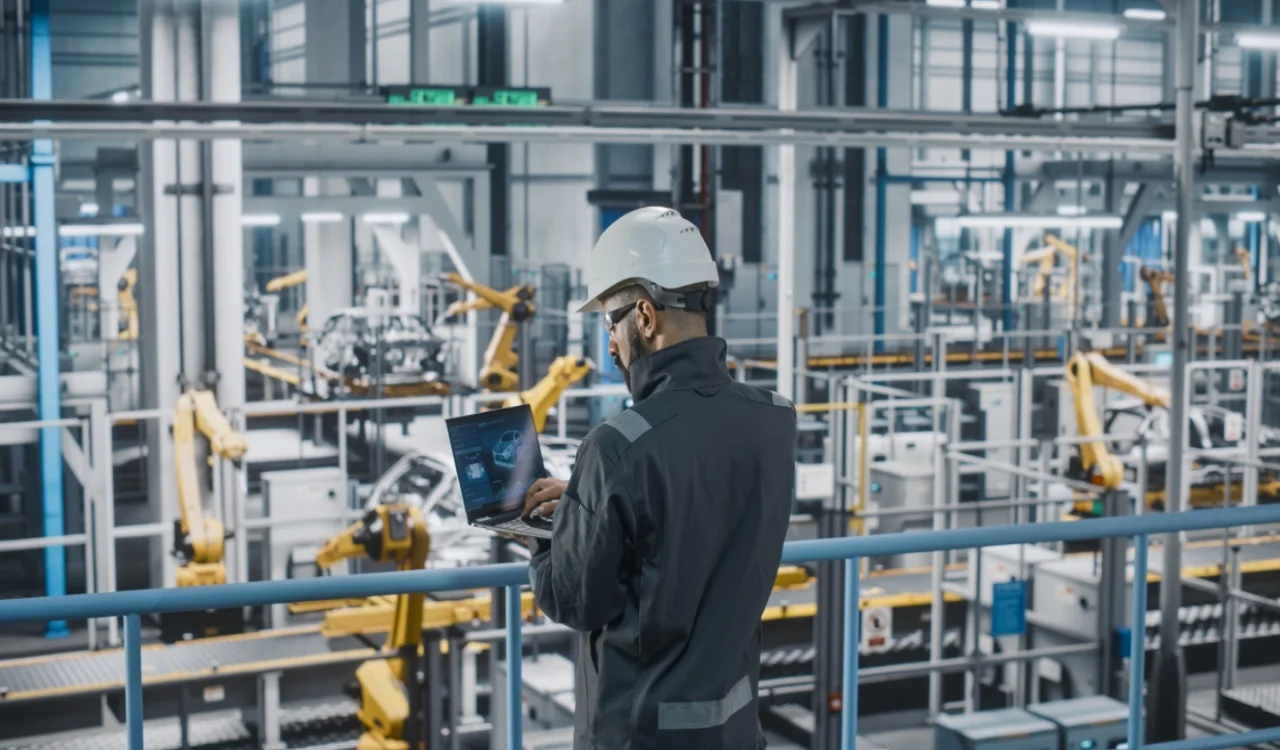
Customers hate it when the product they want to buy is out of stock. It affects brand perception, loses you money and impacts the long-term value generation from individual customers. Understandably, businesses that do not effectively manage their manufacturing supply chains lose revenue right away and customer loyalty in the long term.
This is especially true for global manufacturing supply chains that need to overcome a variety of challenges presented by natural disasters, shifts in global politics, shipping disruptions and much more. Well-oiled supply chains help companies attain a competitive advantage in terms of business efficiency and future preparedness.
This article throws light on the elements, major challenges faced by manufacturing supply chains and how technology helps optimize the operations.
Key Components of a Manufacturing Supply Chain
The success of a manufacturing supply chain depends on the following elements:
Suppliers
A recent study of manufacturing supply chains by Deloitte, cited product issues from suppliers struggling to meet the demand as the second leading operational challenge. Businesses often rely on more than one supplier to ensure cost efficiency and avoid unanticipated delays in the procurement process.
Raw Materials
High quality raw materials are a prerequisite for creating high quality products. As such, it is imperative that businesses strike the right balance between affordability and quality of raw materials.
Production
Production is what usually comes to mind when one thinks of a manufacturing supply chain, and for the right reasons! The production phase is key to optimizing business expenses and meeting customer demand.
Inventory Management
Some companies manufacture products as they are ordered and store them for short periods while others prefer to keep ready-to-ship goods in their warehouses to ensure timely order delivery. Either way, poor inventory management can lead to stockouts that push customers to competitors or to overstocks that increase carrying costs.
Product Distribution
An efficient distribution process sets customer expectations right even before they place the order. This stage is also crucial for enhancing operational efficiency.
Retailers
In addition to purchasing the produce from manufacturers, retailers also provide valuable data on demand and optimal inventory levels to be maintained. This data can be used to forecast demand, monitor market trends and much more.
Maintenance
Product returns, replacements, or repairs can prove costly for companies if the item is out of its warranty period. Tracking such requests can help businesses with spare-parts management, preventive, corrective and predictive maintenance. It enables companies to balance good customer service with cost-efficiency, potentially turning one-time buyers into loyal customers.
Recycling
New-age customers are increasingly preferring sustainable companies. Businesses that are looking to conserve natural resources, reduce waste, and lower expenses need to efficiently recycle materials to reduce the carbon footprint of manufacturing.
As seen above, manufacturing supply chains in recent years have become multi-stage processes with different stakeholders and operations. In addition, they are also interspersed across the globe and are thus prone to crumbling when challenged.
Challenges Faced by Manufacturing Supply Chains
Labor Shortage
Textile and metal fabrication industries in the U.S. recently reported staggering labor shortages. Manufacturing supply chains across many other industries have also been deeply affected by the lack of skilled workers as workforce participation has fallen below pre-pandemic levels.
The implications of labor shortage are not just limited to revenue generation. In addition to not being able to keep up with market demand, a deconditioned workforce made up of new and untrained workers is likely to be more accident and injury-prone. Such workers can also increase the likelihood of product quality issues, product recalls or lawsuits.
Increasing Costs of Raw Materials and Components
Market leaders like P&G, Caterpillar have reported to be grappling with rising material costs forcing them to jack up product prices to the end consumers. Supply chains are becoming increasingly complex global systems.
Freight transport restrictions during the covid-19 pandemic, the Russo-Ukrainian war, political and trade tensions between the U.S. and China, and logistical disruptions like the blockage of the Suez Canal have contributed to the recent surge in prices of raw materials. High component costs not only reduce profit margins but also hinder businesses from meeting consumer demand.
Complex Manufacturing Supply Chains
Supply chain disruptions like the above throw light on the fragility and complexity of today’s global manufacturing supply chains. Stability of these supply chains is heavily reliant on geopolitics. For starters, the U.S. – China trade war badly affected the consumer electronics industry. China banned the export of germanium and gallium, two niche metals crucial to the manufacturing of semiconductors and electronics.
Although this has motivated multiple manufacturing companies to shift to a ’China plus one’ production strategy wherein companies diversify their supplier bases between China and a Southeast Asian country such as Vietnam, Indonesia or Thailand; it has cost the manufacturing industry millions of dollars in losses.
Poor Inventory Management
Inventory is one of the most valuable assets of a business. In addition to having either overly stocked warehouses and paying huge carrying costs or facing stockouts and customer dissatisfaction, poorly managed inventories with inaccurate demand forecasting can also hurt business revenue.
Case in Point
Nike, one of the leading athletic apparel manufacturers, once reported a 14% drop in share prices as the company logged a 44% rise in fiscal first-quarter inventory. The company revealed that the losses were fueled by elevated in-transit inventories due to production issues in the supply chain and imprecise demand management.
Supply chain disruptions cost businesses in the U.S. $228 million annually! Disruptions can arise due to a variety of factors such as natural disasters, pandemics, changes in global political scenarios, economic shifts and much more. Irrespective of the cause, they hinder manufacturing supply chains from operating at full efficiency.
How Technology Reduces Operational Inefficiencies in Manufacturing Supply Chains
Technology and automation can help in demand forecasting, inventory management, eliminating procurement challenges, mitigating disruptions and much more. Here’s a brief overview of how deploying advanced supply chain visibility and analytics technology increases your manufacturing supply chain’s operational efficiency across different stages:
Procurement
Manufacturers can utilize technology to accurately track real-time stock levels for raw materials. Businesses can also automate the order placement process when inventory levels fall below a certain threshold. Enterprise resource planning (ERP) solutions can collect and analyze information (to a certain extent) on supplier performance, pricing trends and other key metrics that are crucial to procurement.
Leading manufacturing companies like Unilever and Siemens use AI technologies to discover and qualify new suppliers before potential crises wreak havoc on their supply chains. They also use it to automate negotiations, analyzing what else existing suppliers can provide and much more.
Production
Many manufacturers incorporate automated robots into their production processes to enhance productivity, operational speed and reduce injuries. Other technologies like 3D printing are often used to reduce material wastage, improve the quality and speed of production.
For example, GE Appliances, a renowned home appliance manufacturer deployed automatic robotic welding with integrated seam tracking technology. This technology enables the robot to precisely detect the edge between the two metals and position the weld in the right place every time.
Product Distribution
Many manufacturers employ warehouse management systems that can build on the accuracy and fulfillment times in the workflow.
For example, Amazon recently announced having over 750,000 robots working collaboratively with their employees at their fulfillment center. The move aims to increase accuracy for delivery estimates, ensure workplace safety, and free up employees by taking on highly repetitive tasks.
Transportation management systems can help in finding optimal shipping routes and sending automated status updates to customers and businesses.
Manufacturing supply chains operating at full efficiency save time, money and business reputation. They are well-equipped to handle risks and other supply chain obstacles.