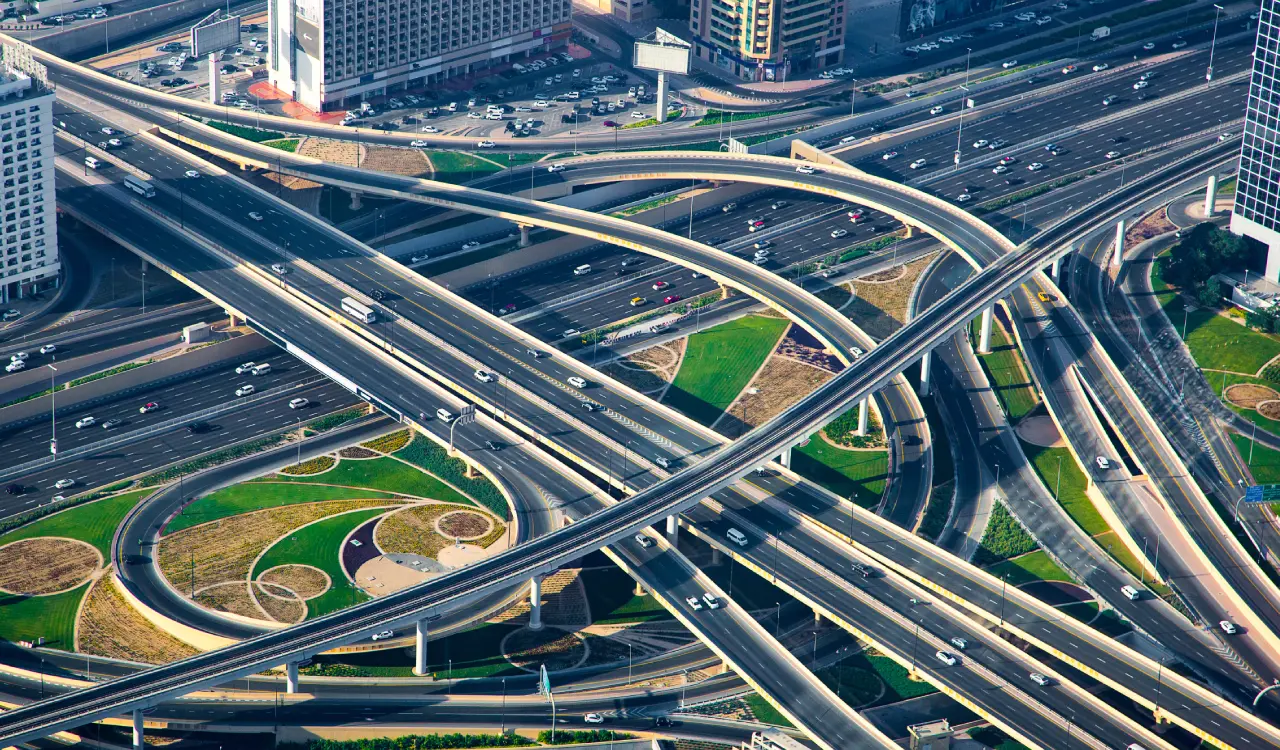
Everything You Need to Know
Supply chain management involves supervision of materials, data, and finances as they move from supplier to manufacturer to wholesaler to retailer to finally the end customer. It entails integrating and directing these movements both within and across the business. Let’s delve further into what is supply chain management and its increased significance in today’s competitive landscape.
Stages of Supply Chain Management Process
The following components of supply chain management are monitored closely to ensure seamless and quality supply chain services.
Planning
Planning is a process where a long-term framework is established for a supply chain management system. Effective planning allows companies to anticipate future demand fluctuations, resource constraints, and potential disruptions. This proactive approach helps them make informed decisions and adapt their strategies accordingly. Planning helps minimize the risk of stockouts or overstocking. It enables enterprises to maintain optimal inventory levels, reducing costs and ensuring product availability for customers leading to high customer satisfaction.
A successful planning process embodies accuracy and agility, effective demand management with the ability to swiftly respond to market dynamics. This entails leveraging real-time data analysis and scenario planning to maintain flexibility. Collaboration and visibility are paramount, necessitating seamless communication and information sharing across all supply chain departments. Moreover, flexibility and scalability ensure the plan’s adaptability to evolving business needs and growth opportunities.
Sourcing
This process involves procuring the essential ingredients ā raw materials, components, and services ā to bring a product to life. But successful supply chain leaders go beyond simply getting the best price. They understand that building strong, strategic partnerships with suppliers is key to a resilient and successful supply chain.
The cornerstone of successful sourcing lies in balancing cost optimization with other crucial factors. While price remains significant, it’s imperative to consider the broader picture, including the total cost of ownership. This encompasses factors such as transportation costs, quality control expenses, and potential disruptions. Supplier reliability and performance are equally vital, encompassing on-time deliveries, consistent quality, and responsiveness to changing needs. Establishing and maintaining strong relationships with dependable suppliers who can meet expectations and adapt to fluctuating demands is key. Additionally, fostering a diverse supplier base mitigates risks associated with overdependence on any single source.
Engineering
The design and administration of systems that enhances the movement of goods and information along the value chain is referred to as supply chain engineering. Numerous decisions, including those on distribution strategy, inventory control, production scheduling, and supplier selection, are frequently involved in these systems. In the engineering stage of the supply chain management process, efficiency and automation are paramount objectives, aiming to streamline processes and minimize waste through automated solutions.
Flexibility and scalability are crucial, enabling adaptation to market dynamics and varying demand levels. Seamless integration with existing enterprise systems for real-time data access is essential, facilitating informed decision-making throughout the supply chain. Additionally, engineering solutions are sought to optimize resource allocation, reduce waste, and streamline logistics operations to achieve overall cost reduction objectives.
Manufacturing
Manufacturing is the stage where the components that have been sourced from suppliers are wielded into products/goods for the consumers. This critical phase involves intricate processes, quality control measures, and strategic decision-making to ensure efficient and high-quality production.
In a robust manufacturing function, maximizing efficiency and throughput is paramount, achieved through optimized production processes and lean manufacturing principles. Quality control measures are rigorously upheld throughout the production process to ensure consistent product quality and customer satisfaction.
Adaptability to changing market demands and product lifecycles is crucial, driving the need for agile manufacturing systems capable of quick adjustments. Seamless integration across supply chain stages and real-time data visibility enable informed decision-making and proactive issue identification within the manufacturing process.
Learn More: The Evolution of Supply Chain Management
Delivering
This stage involves processing customer orders to select distribution strategies and logistics. The delivery stage entails everything ranging from processing customer orders to selecting distribution strategies and transportation options. This stage also includes warehousing and inventory management.
Effective warehousing and inventory management play vital roles in order fulfillment, while reliable transportation and logistics partners ensure on-time in-full deliveries. Maintaining visibility and communication with customers throughout the delivery process fosters trust and reduces inquiries, emphasizing the importance of real-time tracking and proactive communication.
Returns Management
This is a trial or warranty period where customers can return defective or unsatisfactory products. These products are assessed and restocked, refurbished, or disposed of based on their condition. An effective returns management system is crucial for minimizing financial losses, enhancing customer satisfaction, and fostering brand loyalty. It should prioritize a simplified return process, efficient logistics, thorough product inspection, and transparent communication with customers.
Additionally, data analytics enable continuous improvement by identifying trends and root causes of returns. Investing in such a system not only streamlines processes and reduces costs but also provides valuable customer insights, potentially turning negative experiences into opportunities for building trust and loyalty.
Monitoring
Enterprises continuously track and trace their supply chain management services through various key performance indicators (KPIs) such as:
- Inventory Turnover
Measures how efficiently inventory is managed, aiming to minimize holding costs and stockouts. - On-Time Delivery Rate
Tracks the percentage of orders delivered to customers by the promised date. - Order Fulfillment Cycle Time
Measures the time it takes to process and fulfill a customer order. - Production Efficiency
Evaluates how effectively resources are utilized during production. - Transportation Costs
Tracks the cost of transporting goods throughout the supply chain. - Supplier Performance
Monitors factors like on-time deliveries and quality from suppliers. - Customer Satisfaction
Tracks customer feedback regarding order fulfillment, product quality, and overall experience.
Leveraging data analytics tools for insightful reporting enables data-driven decisions to optimize processes and resource allocation. Benchmarking against industry standards and fostering collaboration and communication across departments further promote continuous improvement within the supply chain.
Read More: Check Out Our Supply Chain Glossary: 470+ Terms and Definitions
The Importance of a Successful Supply Chain Management
In today’s globalized world, smooth operations are no longer a luxury, they’re a necessity. This is where successful supply chain management (SCM) comes in. By effectively orchestrating the flow of goods and services, SCM offers a powerful advantage, driving not only efficiency but also significant financial benefits. The current supply chain services market is valued at 20.27 billion US dollars and is projected to grow up to 47.29 billion by 2029, exhibiting a CAGR of 12.1% during the forecast period (2022-2029). Let’s delve into why successful supply chain management is crucial for business success.
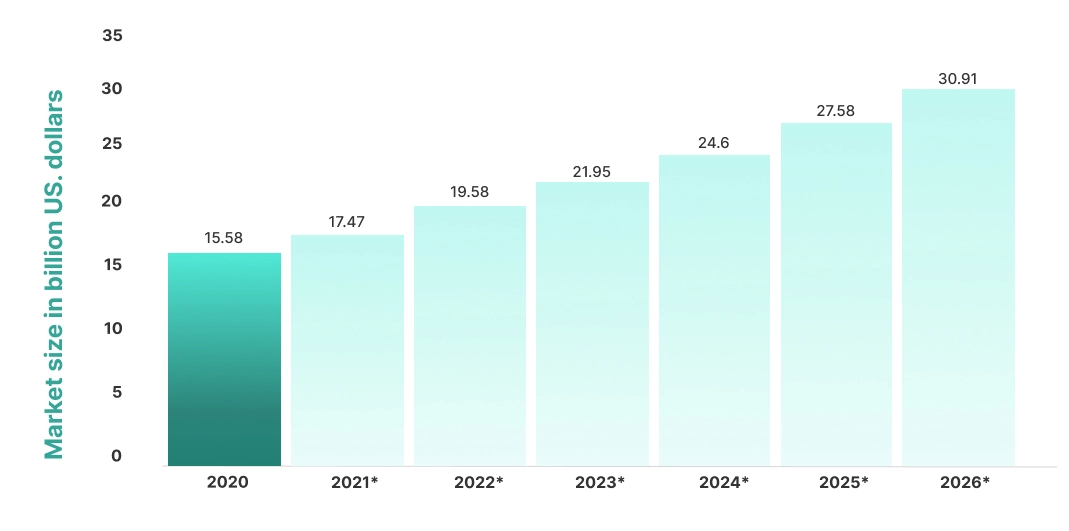
- Higher Efficiency in Supply Chain Management
Businesses can avert delays by implementing backup plans, such as acquiring supplies from a second source, thanks to real-time data on raw material availability and manufacturing delays. In the absence of real-time data, businesses frequently face issues such as out-of-stock inventory or delayed shipments to final customers. Enhanced efficiency is another benefit of implementing intelligent automation technologies. Studies show that 57% of companies believe that supply chain management gives them a competitive edge. - Reduced Operational Costs in Supply Chain
Management
Organizations can reduce operations costs by leveraging AI and ML technologies, and automation that reduces manual work and provides opportunities for future improvements and improved decision making. - Effective Risk Management
Businesses can effectively manage interruptions if they anticipate and evaluate the risk. Predictive analysis, which provides end-to-end visibility and helps identify problems and reduce risk, is frequently used in the supply chain. This can be used by businesses to improve accuracy, flexibility, and efficiency in various processes, such as supply and demand planning, product development, etc. As a result, it enhances the value-chain nodes, potentially benefiting the enterprise. - Enhanced Customer Experience
An effective supply chain equals happy customers. Modern customers demand seamless omnichannel experiences, greater product customization, and faster delivery times. According to a report, 70% of companies believed that supply chains are a key driver for quality customer service. - Visibility/Transparency in Supply Chain Management
Visibility is one of the essential elements in supply chain management. It provides all the parties involved in the supply chain process (suppliers, manufacturers, retailers, wholesalers, and consumers) to track the supply chain process with transparency and enables decision-making. - Demand Forecasting/Prediction in Supply Chain
Management
An effective supply chain helps businesses predict disruptions beforehand and minimizes or even avoids the impact that it would have on the supply chains. This helps the companies deal with less losses while keeping the supply chain process seamless and agile.
Supply Chain Management Risk Assessment: Exploring the Impact on Operations
Impact of Inflation in Supply Chain Management
Rising input material costs due to unpredictable events such as conflicts or logistical issues squeeze profit margins. Beyond external factors, even internal supply and demand fluctuations can cause raw material price changes. This forces businesses to re-evaluate sourcing, negotiate with suppliers, and potentially adjust production, all while navigating a more expensive operational landscape.
Case in Point
During a 2022 earnings call, the COO of Procter & Gamble stated that the company would implement price increases on its Baby Care, Feminine Care, and Adult Incontinence product categories in the US to neutralize a portion of the impact of rising commodity costs.
Impact of Global Tensions on Supply Chain Management
Supply chain management includes handling demand fluctuations and unforeseen disruptions caused by geopolitical issues, trade restrictions, and numerous other challenges. For instance, the semiconductor shortage that caused lack of necessary electrical components is currently generating significant delays and disruptions in the automotive supply chain. The implications of this scarcity are extensive; since the first half of 2020, automakers have had to cope with launch schedules and significant revenue losses. These include production halts, decreased vehicle inventories, and altered consumer experiences.
- Numerous firms worldwide have experienced a shift in their business environment due to the COVID-19 pandemic. This has brought to light the significance of responding, adjusting, and establishing crisis management protocols to handle unforeseen circumstances.
- Global supply networks often face disruptions by tariffs and trade tensions. For instance, trade barriers resulting from disputes between major economic countries may impact the supply of automobile components and parts. Geopolitical tensions between the U.S.-China, and Japan-Korea are a few examples.
- The attacks on Red Sea shipping routes which have severely affected shipping through the Suez Canal, added to existing geopolitical and climate-related challenges. Additionally, diminished water levels in the Panama canal have raised concerns about the long-term resilience of global supply chains, underscoring the fragility of the world’s trade infrastructure.
Sustainability in Supply Chain Management
Consumers are increasingly becoming vocal about environmental responsibility, and businesses are responding by incorporating eco-friendly practices throughout their supply chains.
- Sustainable sourcing
Enterprises are looking for suppliers who comply with responsible practices such as, ethical sourcing and strict welfare standards. For instance, Etsy promotes local and community-centric enterprises, actively endorsing small-scale producers and artisans. Through this, Etsy diminishes the environmental footprint linked with extensive shipping and large-scale manufacturing. By prioritizing local sourcing and production, Etsy facilitates the establishment of sustainable businesses for sellers, fostering economic growth within their communities. - Waste management
Minimizing packaging and using reusable materials help cut down on waste generation. Companies are finding innovative ways to reuse waste materials. Nike, for example, uses recycled polyester from plastic bottles to create yarn. In addition to reducing waste, recycled poly lowers carbon emissions by up to 30 percent and diverts an average of 1 billion plastic bottles annually from landfills and waterways. And the Alibaba Group and Unilever have partnered to build the first extensive closed-loop plastic recycling system in China. The collaborative project, named Waste-Free World, is a component of Unilever’s effort to address the underlying causes of plastic waste and adopt new packaging principles. The companies have set a goal to reduce their use of virgin plastic, cut plastic packaging by more than 100,000 tonnes and accelerate their use of recycled plastic by 2025. - Reducing carbon footprint
Shifting to renewable energy sources like solar or wind power for manufacturing facilities significantly reduces greenhouse gas emissions. Apple is a prime example, investing in solar energy to power their data centers. More than 18 gigawatts of clean electricity now power Appleās global operations and manufacturing supply chain. And DHL, a major logistics company, is investing in electric delivery vehicles and exploring alternative fuels for their fleet.
Fill out the form below to connect with our supply chain experts & schedule a free demo!